When a specific error occurs and your Honeywell Smart Valve can diagnose it, your unit’s LED lights will flash in a particular sequence. That is an error message. Unlike most appliances, you won’t see letters flashing on your screen.
To get rid of these warning flashes, you need to first know what each error message represents and its solutions. So, let’s get started with our simple and easy Honeywell Smart Valve Codes troubleshooting guide.
Table of Contents
- Honeywell Smart Valve Codes [7 Easy Solutions]
- Error: 2 Flashes
- Error: 3 Flashes
- Error: 4 Flashes
- Error: 5 Flashes
- Error: 6 Flashes
- Error: 6+1 Flashes
- Error: 6+2 Flashes
- FAQ:
- How does the Honeywell smart valve work?
- How do I know if my furnace gas valve is bad?
- What is a 100-shut-off system?
- How much does it cost to replace a flame sensor?
- How do you adjust inlet gas pressure?
- Conclusion
Honeywell Smart Valve Codes [7 Easy Solutions]
In this section, we’ll explore the meaning of each error message and its easiest solutions.
Error: 2 Flashes
Your Honeywell Smart Valve signals two flashes after a call for heat begins and the airflow-proving switch remains closed for more than 30 seconds. The combustion air blower is not turned on until the airflow proving switch is turned on.
Note: You can also read how to fix Honeywell Surround Heater shuts off issue.
Solution:
Start by checking to see whether the airflow proving switch is locked in the closed position. The switch may need repair or replacement. In case the airflow proving switch isn’t stuck, it could be a miswired or jumpered switch.
Take a look at the Honeywell Smart Valve wiring diagram below, to fix any issue with the wiring of your unit. Cross-check the wiring of your unit with this image. Make any necessary changes.
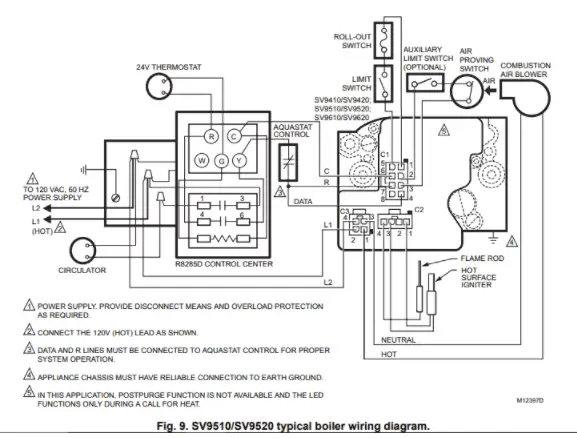
Error: 3 Flashes
This error code means that after the combustion air blower is turned on, the airflow proving switch remains open for more than 30 seconds. With the combustion blower turned off, the system enters a 5-minute delay period. A new ignition cycle will commence at the end of the 5-minute wait.
Solution:
To get rid of this error try the following steps.
- Make sure the ignition system control switch is turned on.
- Switch functioning, tubing, and wiring to demonstrate airflow.
- Improper combustion airflow due to obstructions or restrictions in the appliance’s air intake or exhaust flue system.
Error: 4 Flashes
If you’re getting 4 flashes, your limit string is open. The blower for combustion is turned on. The heating speed circulating air fan will be engaged until the limit string resets if the control system incorporates an ST9160 Electronic Fan Timer.
Solution:
You need to go through the following steps to ensure a well-functioning unit and to fix the error message.
- Turn on the manual or automatic burner rollout switch.
- Switch on the auxiliary limit switch or the high-temperature limit switch.
- In good working order and properly connected limit and rollout switch wiring.
Error: 5 Flashes
This error message means, your unit’s flame signal was detected out of order. The combustion air blower is turned on. The heat speed circulation air fan will be powered after the selected heat fan is on delay if the control system incorporates an ST9160 Electronic Fan Timer.
Solution:
You need to make sure that the flame is going strong at your main burner. If the main burner does not light after the pilot has been lit and the igniter is turned off, you need to take the following actions.
Step 1: Make sure the pilot flame and the flame rod are in good contact. Inspect the pilot burner bracket isn’t twisted or misplaced from its original position.
Step 2: Check for proper entrance gas pressure with a gas pressure reading instrument (e.g., a manometer). For this measurement, there is an outlet gas pressure tap on the outlet side of the gas valve, as well as an entrance pressure tap. Look at the appliance’s rating plate to confirm the pressure required for proper operation.
Step 3: Examine the pilot orifice for any obstruction or visible damage. Replace the orifice if necessary; DO NOT attempt to drill it out.
Step 4: Use a jumper cable to check the electrical system for a good system ground through the pilot burner gas tubing (with alligator clips). If the system works after connecting one end of the cable to the pilot burner bracket and the other end to the gas valve, you’ve isolated the problem to the poor or insufficient ground.
Step 5: If none of these inspections reveal a fault with the system, replace the ignition assembly. The system should now function properly; if not, replace the Smart Valve.
Error: 6 Flashes
When the system is in a lockout, this error message will appear. If the call for heat is still there after a one-hour lockout reset wait, the control will reset and commence a fresh ignition sequence.
The reasons why this may happen are the gas supply is off or at too low a pressure, the HSI element is damaged or broken, the line voltage HOT lead wire is not connected to the L terminal on the ST9160 or Terminal Board, the appliance is improperly grounded, the flame sense rod is contaminated or in the wrong place, and the HSI element is in the wrong place.
Solution:
You need to check that the above causes are fixed. If your unit doesn’t have any of these issues, then, verify that the hot surface element and flame sense rod wire are in good working order and linked appropriately. The error message should top appearing at that point. In case it’s still there, contact a professional to help you.
Error: 6+1 Flashes
The maximum trial for ignition during a call for heat that the unit allows is four. When this limit is exceeded, your unit will enter soft lockout mode. Also, this error warning will start flashing. The following are the most common causes behind this error message.
- Inconsistent or insufficient gas supply pressure to operate this unit when other gas appliances are in use.
- Appliances and power supplies are not earth grounded properly.
- Contaminated flame sense rod, grounded to appliance chassis, or in the wrong location.
Solution:
After ensuring that the above issues are fixed in case they were present in your unit, your error message should disappear. However, if it persists, Make that the HSI element and the flame sense rod wire are in good working order and linked appropriately.
Error: 6+2 Flashes
In case, your unit’s flame sensor was lost during a run and then the recycle count crossed 5, this error message will flash.
Solution:
Do the following for Honeywell smart valve troubleshooting.
- Check for inconsistent or insufficient gas supply pressure when other household appliances are in use. Contact your gas utility company if this is the issue.
- Ensure that the appliances and power supplies are earth-grounded properly.
- Inspect whether the unit has a contaminated flame sense rod, grounded to appliance chassis, or in the wrong location.
- Verify that the HSI element and flame sensor rod wiring are in good working order and connected appropriately.
FAQ:
How does the Honeywell smart valve work?
The pilot gas is ignited by a 24 VAC-powered hot surface pilot gas igniter in the Smart Valve system. It’s self-contained, so there’s no need for a separate ignition source, which is generally found in the furnace or boiler vestibule.
How do I know if my furnace gas valve is bad?
If you don’t hear that small clicking sounds the internal valve makes when 24 volts are applied to the gas valve terminals from the board, you may have a defective gas valve.
What is a 100-shut-off system?
Both the pilot valve and the main gas valve are turned off and closed when the flame-proving device system fails.
How much does it cost to replace a flame sensor?
The cost of repairing or replacing a flame sensor ranges from $75 to $200.
How do you adjust inlet gas pressure?
Turn the gas pressure adjustment screw clockwise to raise the pressure and counterclockwise to lower it. If your furnace has two stages, you’ll need to set gas pressure for both the low-fire and high-fire modes.
Conclusion
Now that you know how to troubleshoot Honeywell Smart Valve codes, hopefully, your Smart Valve will be fixed in no time. Leave us a comment below in case you have any questions.